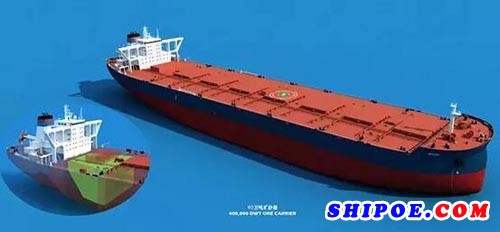
隨著上海外高橋造船有限公司40萬噸超大型礦砂船(VLOC)的開工,該公司在生產過程中的厚板焊接工作量大幅度增加。為此,在外高橋造船組立部提出需求后,該公司工藝研究所對礦砂船甲板分段49毫米厚板焊接工藝積極進行了創新研究,以實現設備利用最大化、效益最大化,同時強化厚板焊接質量。
老工藝:采用埋弧焊機進行單面焊接,將厚板拼接后安裝縱骨,然后到外場翻身碳刨,在反面再進行埋弧焊接,即“SAW(正面)+SAW(反面)”的焊接模式;
新工藝:使用流水線FCB焊接設備進行單面焊接,將厚板拼接后安裝縱骨,然后到外場翻身焊接反面埋弧焊,即“FCB(正面)+SAW(反面)”的焊接模式。
目前,該工藝已通過工藝評定,并應用于現場厚板焊接作業。在生產效率方面,新工藝投入使用后,依托流水線自動化程度高和FCB焊接設備效率高、質量穩定的優勢,打破了原工藝采用埋弧焊速度較慢的制約瓶頸;此外,新工藝對坡口形式進行了優化,將“X”型改為“Y”型坡口,厚板反面碳刨的深度減少10毫米,直接減少了焊接工作量,明顯縮短了礦砂船分段生產周期;在經濟效益方面,相較“SAW+SAW” 工藝采用進口焊材施工,“FCB+SAW”新工藝實施后,當FCB、SAW均采用進口焊材時,單船僅厚板焊接成本將實現較大幅度節約。這也為礦砂船批量建造節省更多的成本打下了基礎。
據悉,外高橋造船正深入開展“埋弧焊使用國產焊材”的工藝研究。經測算,當FCB采用進口焊材、SAW采用國產焊材時,則單船厚板焊接成本比原方案實現較大幅度節約,經濟效益顯著。