據央視新聞報道,全球最大液化天然氣項目——亞馬爾項目的最后核心模塊,8月16日在青島裝船起運,這意味著我國成功掌握液化天然氣核心建造技術,進入國際液化天然氣建造第一梯隊。
隨著十幾層樓高、重達一萬多噸的壓縮機模塊裝船運往北極,我國首次承攬的36個,總重18萬噸的液化天然氣核心模塊全部建成。
亞馬爾項目是中俄當前最大的經濟合作項目,也是全球首例極地天然氣勘探開發、液化、運輸、銷售一體化項目。項目位于北極圈內,最低溫度達零下52攝氏度。為縮短工期及節省建設成本,大部分建筑均采取模塊化方式建設。
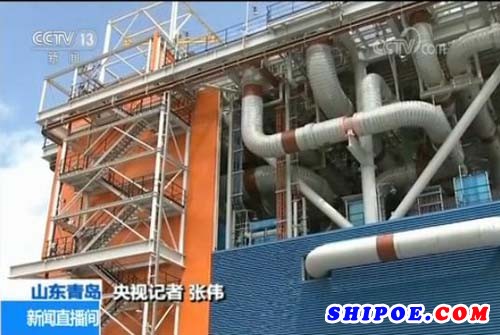
中國海油承擔了整個項目的的“心臟”模塊,總價超過100億,這些模塊內部構件種類之多、數量之大,對精度要求之高,施工工藝之復雜,遠超行業同類項目。鋪設的管線全長超過20萬米,相當于北京六環長度;鋪設電纜330萬米,可以從北京連接到北極圈;完工文件達700萬頁,可以填滿兩個車庫。
亞馬爾項目設計年產天然氣280億立方米、凝析油100萬噸。項目全面建成投產后,每年將至少有400萬噸液化天然氣銷往中國市場。
嚴寒是整個亞馬爾項目需要面對的最大困難,對此,中國企業打破國外技術壟斷,突破一系列施工和技術難題。
亞馬爾項目地處極寒地帶,所有關鍵裝備和管線都要穿上特制的保溫服——泡沫玻璃。泡沫玻璃切割在工程中是特別重要,一旦泡沫玻璃出現問題了,整個項目就會出現災難性后果。而這一特殊材料切割技術被新加坡等少數國外公司長期壟斷。
成立泡沫玻璃切割機科研課題組,自主研發切割技術,經過五個月的不斷實驗,世界上第一臺泡沫玻璃半自動切割設備成功誕生。相比手動切割,效率提升了3倍不說,將材料切割損耗由50%降到28%。僅此一項,就節約成本4000多萬元。
深冷保溫材料切割技術自主研發、焊接技術獲得突破、涂裝工藝打破國際壟斷……一項項技術突破,讓亞馬爾項目得以成功建造,使中國海油工程實現了由單一產品到項目總包、由低端制造到高端制造的跨越式發展,中國也由此躋身國際液化天然氣模塊建造“第一梯隊”。