1月15日,振華重工首臺通過流水線裝配完成的減速箱在南通傳動公司下線。
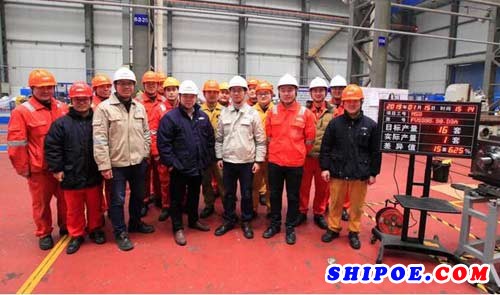
該流水線主要用于裝配大車減速箱。流水線采取分叉式設計,共設置10個工位,上料段兩條支線分別完成齒輪齒軸上線、軸承和齒輪熱套、初步安裝、調試和箱體上線工序,匯合后完成齒輪齒軸安裝、齒面嚙合檢驗和合箱等工序作業。經初步測試,首臺減速箱生產共用時2小時左右。在測試安裝過程中,測時和檢驗人員對各工序進行了跟蹤、記錄,運行數據將為后期優化提供支撐。預計在對各工位工序進行精準調整后,有望實現日產16臺減速箱的目標。
多年來,客戶差異化的需求,同時受減速箱大型化的限制,讓減速箱生產一直實行傳統的“定點”裝配的方式,在固定的地點完成全部減速箱的裝配作業,往往導致了在制品庫存的增加,裝配效率較低。隨著近年來振華重工標準化步伐的加大,特別是自動化碼頭設備時代的到來,讓標準化制造、流水線生產成為可能。以標準化程度高的小型減速箱為試點,2016年至2018年南通傳動公司先后推出了大車減速箱涂裝流水線、齒軸柔性智能化生產線、小型零件精加工生產工段等,提升了生產效率,縮短了生產工期,提高了產品質量和現場管理水平。