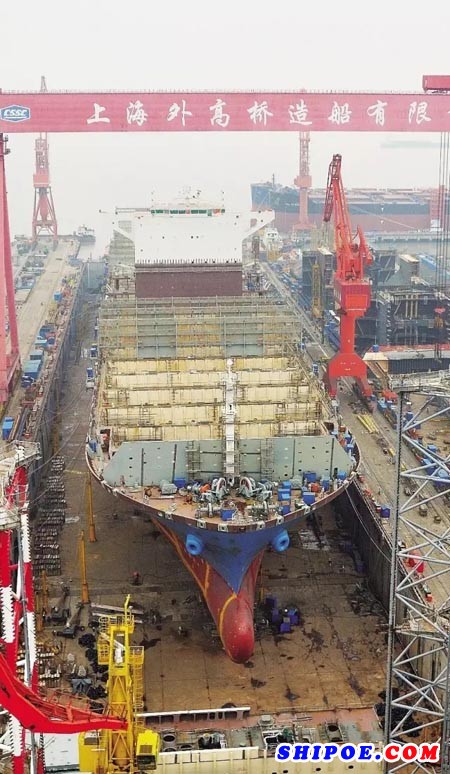
2013年7月,外高橋造船和中國船舶工業集團公司第七〇八研究所以及中國船舶(香港)航運租賃有限公司結合國際航運市場的最新發展趨勢,精誠合作,致力打造新一代超大型集裝箱船。三方簽署3艘18000TEU集裝箱船建造合同,其承租運營方為國際航運界三大班輪公司之一法國達飛海運集團。目前,經過眾多船舶建造師、設計師的共同努力,這3艘18000TEU集裝箱船已經在外高橋造船及其控股的上海江南長興重工有限責任公司廠區相繼交付。該型船的多項指標創下了中國造船業新紀錄,并在多項關鍵技術上取得重大創新成果。相信在未來,超大型集裝箱船將成為外高橋造船的“拳頭產品”,通過不斷的研究、實踐,外高橋造船將開發出更多創新型超大型集裝箱船建造工法。
攻堅克難 迎接挑戰
當前,國際航運市場已進入“大船時代”,造船業也在不斷研發新型超大型船舶,國際知名船企之間展開了新一輪的角逐。超大型集裝箱船不僅是未來中歐航線的主力船型,而且是“海上絲綢之路”的關鍵裝備。長期以來,韓國造船企業憑借其研發和建造技術優勢,壟斷了10000TEU以上集裝箱船這一船舶領域的高端技術,而在國內,包括長興重工在內的個別船企雖有過批量建造8530TEU、9400TEU等萬箱級大型集裝箱船的經驗,但在18000 TEU級集裝箱船的建造領域卻從未有過嘗試。因此,合理設計、突破并掌握超大型集裝箱船的關鍵工藝,順利建造交付該型船,對企業來說仍是嚴峻的挑戰,也受到了眾多專業人士的關注與期待。
“達飛·瓦斯科·達伽馬”號是18000TEU集裝箱船系列船中的首制船。這一海上“巨無霸”作為中國船舶工業集團公司實現轉型升級、大力發展高端船型的突破口之一,將進一步提升中船集團的品牌影響力,提升外高橋造船的市場競爭力。這也讓參與該項目的每一位設計師及建造師都肩負著重大使命。
凡事預則立,不預則廢。外高橋造船及七〇八所的研發團隊充分發揚敢打敢拼的精神,不斷優化設計方案、狠抓建造精度與生產節點。研發團隊調研了班輪公司對船型的各類需求后,在各設計專業間分專題、按難點進行了多次協調,不斷優化最初方案,以求達到該型船總體性能上的平衡和提升。在設計過程中,研發團隊摒棄了閉門造車的做法,提出了專業化合作的思路,通過與船級社、船廠以及設備供應商展開合作的方式,開展技術和系統集成,做到了出圖完備、修改少,為后續的建造打下了堅實的基礎。此外,研發團隊在該船設計階段就對綠色環保問題作了諸多考慮,該型船不僅滿足MARPOL燃油艙保護的要求,在設備和材料的選型方面,還兼顧國際海事組織(IMO)的綠色拆船公約要求,合理地控制整個生命周期內對環境的影響,達到環境友好型的綠色集裝箱船型標準。
在建造階段,為了滿足船東的需求,首先,在總體布置上,該船采用雙島式上層建筑,駕駛室和生活區位于船的前部,機艙位于船的后部,燃油艙布置在生活區下方。駕駛室位于前部,提升了船員的可視性。其次,由于該船航速較高,舵空泡及螺旋槳槳轂空泡都會對舵產生剝蝕。為有效降低空泡剝蝕的風險,該船采用了全懸掛導邊扭曲舵,可以利用槳后的旋轉水流,在一定程度上降低功率消耗。同時,該船采用當時最先進、能耗最低的MAN B&W 11S90ME C10.2主機。主機的缸套水和汽缸油都采用了德國曼恩集團(MAN)的最新技術,以降低主機運行時的能耗。設計方面還做到了充分利用主機的余熱,使船舶在正常航行中,在淡水的制造、燃油的加熱等方面能完全利用主機的余熱。
此外,船東、船檢對焊接技術和質量的要求極為嚴格,18000TEU集裝箱船抗扭箱部位所使用的是長度達到17米多、厚度達到85毫米的高強度鋼板。面對這項前所未有的挑戰,外高橋造船及時開展了高強鋼焊接技術培訓工作,對公司所有焊工崗位實行考核上崗制度。同時,外高橋造船還與中國船級社(CCS)開展技術合作,引進了最新型的圖譜探傷儀器,對全船的焊接質量進行嚴格把關。通過大量的焊接試驗以及對高強度鋼大厚板的焊接性進行研究,外高橋造船完成了全套WPQR、WPS的編制,并取得了船級社認可,指導現場施工,并采用TOFD檢測技術解決其無損探傷難題。
上述總體布置、主機油耗優化、高強度鋼大厚板焊接等技術均是外高橋造船在該船建造過程中自主創新的工法。通過攻堅克難、創新研發,外高橋造船全面掌握了超大型集裝箱船建造的關鍵技術,這些創新成果的取得為后續系列船乃至其他超大型集裝箱船的建造積累了寶貴的經驗。
技術創新 打造精品
獨辟蹊徑,創新關鍵技術,以精益求精的工匠精神打造精品工程,是外高橋造船鑄造企業品牌形象過程中一直恪守的宗旨。外高橋造船是國內18000TEU集裝箱船建造領域“第一個吃螃蟹的人”,在該船的建造過程中,外高橋造船研發出的多島建造及大型總段移位工法,綁扎橋立式總組、TOFD檢測技術、模擬吊箱試驗、數字化船塢及專用精度測量工具、橫艙壁導軌架反頂安裝小車等14個主要技術創新點在國內同行中均屬首創。
在18000TEU集裝箱船建造過程中,外高橋造船研發團隊和建造師們充分發揮自主創新精神,依靠技術進步和工法創新,在確保質量的同時,努力縮短建造周期。他們采用綁扎橋立式總組,突破“高空作業低空化”的束縛。18000TEU集裝箱船全船共設有27座綁扎橋,單個綁扎橋來貨為兩榀,采用綁扎橋立式總組,不僅少占用總組場地,而且總組可以在平臺上完成結構對接、舾裝件安裝、涂裝等一系列作業,實現綁扎橋的快速搭載,在很大程度上解決了生產場地空間不足的問題,同時提高了生產效率。
此外,超大型集裝箱船需搭載并安置上萬個集裝箱,其精度控制成為最大的建造難點,尤其是分段艙容、導軌架尺寸等,稍有差池就會影響到整船的質量和作業安全。外高橋造船在生產準備階段就組織開展了大量的技術調研,通過前期策劃梳理出精度控制要點,明確精度控制標準;在建造過程中不斷加強控制,保證控制措施得到嚴格落實,測量操作規范;對分段加工精度進行認真的計算和推導,研究制定了嚴格的控制手段。該船開工之后,從鋼板切割到部件加工,再到小組立、大總組都有專人進行記錄、跟蹤,外高橋造船針對全船近400個分段的各道工序,努力減少誤差積累,確保精度控制。在該船入塢搭載后,外高橋造船采用全站儀測量與計算機模擬相結合的先進方法,在國內造船業中首次實現了數字化試箱技術,經船東實箱抽檢,合格率達100%,全船導軌架開刀修正數量僅為個位數,達到了國內集裝箱船建造領域的最先進水平。
該型船數字化船塢及專用精度測量工具的使用是一大創新亮點,不僅提高了精度測量的效率及準確性,而且完善了精度管理系統。首先,通過建立起規范化的數字化船塢技術搭載網絡體系,旋轉標靶等硬件設施逐步完成了標準化建設,實現了坐標系固化并能長期利用。其次,依托高精度測量的全站儀和先進的精度管理軟件,通過船塢實測作業坐標系集裝箱船本體理論坐標系的有效轉換,統一基準控制所有定位數據,借助全站儀中精度軟件在現場自動得出偏差值,使總段搭載定位能夠更加精確、迅速。再次,持續從積累數據中分析并優化設計下料尺寸,減少分段制作及總段搭載過程中的無謂修割,確定精確的精度補償量來指導現場作業,提高了生產效率。此外,模型堆箱試驗、模擬吊箱試驗,減少了船塢、碼頭試箱試驗工作量;圓心測量工具等一系列專用工藝裝備的開發,降低了作業難度,提升了作業效率,提高了作業安全性;有限元模擬吊裝分析,促進吊裝及加強方案最優化,排除安全隱患及設計冗余等,保障了作業安全及建造精度。在18000TEU超大型集裝箱船的建造過程中,這些關鍵技術共被授權實用新型專利13項,受理實用新型專利4項、發明專利2項,此外還有14篇專業相關論文發表。
18000TEU超大型集裝箱船的研究攻關、建造交付,使外高橋造船掌握了超大型集裝箱船建造的核心技術,形成了一整套圖紙及工藝文件,打造了國內超大型集裝箱船建造基地,培養和造就了一支攻堅克難的技術團隊,進一步推動了我國在超大型集裝箱船領域的關鍵技術集成和技術創新。該系列船的順利交付表明,外高橋造船在建造超大型集裝箱船的管理能力上已進入世界造船業的第一方陣,其在質量、效率、安全、環境以及現場管理方面的水平已得到國際一流船東的認可,這為中船集團旗下企業乃至中國船企承接超大型集裝箱船訂單創造了有利條件。