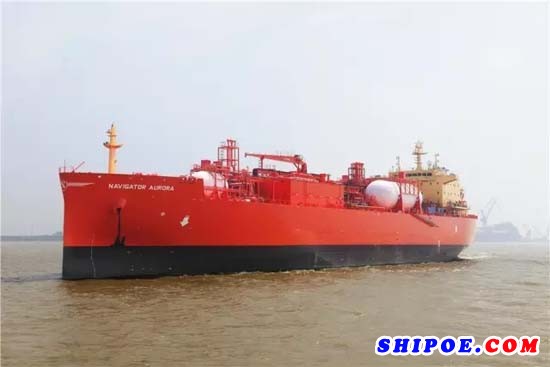
回首“Camel E”首制船的研發、設計、建造歷程,江南造船的相關參與人覺得有酸亦有甜。
1能造還是不能造?
英國航海人氣體運輸公司(Navigator)是江南造船的老朋友。2012年4月,雙方簽訂了5艘2.1萬立方米LEG船建造合同。同年11月,該船東又向江南造船提出一個構想,希望建造一型3.8萬立方米的乙烯、乙烷運輸船,同時,船東對船的主尺度提出了明確的要求——船舶總長不能超過180米。
不超過180米是出于對船舶港口靠泊的考量。總長180米是什么概念?“是1艘中型液化氣船(MGC)的尺度,當時全球最長的MGC的長度是183米,而我們這一型船艙容更大,但總長更短。”江南造船研發人員介紹道。2000年,江南造船承建的2.2萬立方米LEG船總長170米,2012年簽約建造的2.1萬立方米LEG船總長160米。如今,船舶總長增加了20米,但艙容提高了60%以上。
首先要確定的,是采用哪種液罐型式。“考慮到乙烷、乙烯快速裝卸的需要,那只能是可以承受壓力的C型艙。”江南造船產品開發部負責人介紹,在2012年年底,當時已經有非常成熟的3.8萬立方米液化氣船,但船上使用的是不能承受壓力的A型艙。
勾了C型艙這個單一選項,更多的問題衍生出來。C型艙的壓力容器通常選擇的是承壓能力更強的圓柱型、球型封頭,如果沿用傳統做法,很難實現有限空間下3.75萬立方米的總艙容。碟型封頭——這是研發團隊的第一個想法,這種設計能夠大幅節省封頭處空間,極大提高船體的艙容利用率。同時,一改之前液化氣船4個液貨艙的設計方案,該船采用全新的三艙布置設計。
3個C型艙的總體艙容為3.75萬立方米,這就意味著單艙裝載量要超過1.2萬立方米。在此之前,全球單艙容量最大的液化氣船就出自江南造船,單艙容積在6000立方米以內,這一次直接要超過世界紀錄一倍。這個方案提出后,船東、江南造船內部的一些技術人員都抱持懷疑態度。這么大的液罐,壁板厚度要多大?單罐有多重?這么大的液罐裝船后船舶的總體穩性如何?項目研發團隊又開始了新一輪的可行性計算分析。
在此之前,江南造船沒有開展過液罐的設計工作,為此,研發人員獨立自主開發了計算液罐板厚和重量的軟件。經過詳細的分析計算,液罐外殼的最厚處達到了35毫米左右,比江南造船以往建造的液化氣船的液罐厚了十余毫米。
“這么厚的液罐,能造嗎?”技術人員詳細分析了江南造船曾經建造過的LEG船,雖然其液罐的外殼較薄,但加強環的腹板和面板的厚度也都達到45毫米,既然這個厚度能施工,新船型液罐外殼應該也可以。同時,技術人員在不增加板厚的情況下,提高腹板的高度、面板寬度,以此增強新船型罐體加強環的結構強度。
對當時的可行性論證過程,該項目研發負責人至今仍記憶猶新,在船東提出建造構想的4個月后,江南造船通過前期可行性研究,決定正式開始新船型的研發工作。
2給租家提供方案
在研發初期,沒有任何類似的船型技術資料可供參考,技術人員就運用偏差和置信度分析的方法,開展了大量的基礎計算和分析工作,結合先進的船體線型CFD計算分析工具,化解了快速性、穩性和總布置之間的各種矛盾和沖突,最終推出了幾近完美的總體設計方案。
2013年4月,研發人員著手對船體結構、液貨系統和機電系統進行計算分析及驗證,保證了船體與液罐的結構具有較強的安全性,液貨系統的配置相較于以往的設計更加合理,機電系統的設計采用了最先進、能耗最低的ME-GI雙燃料主機。至此,整個船型的技術方案基本成型。
2013年的4~5月,研發人員經常是下班后又陪著在倫敦的船東上班。“船東從租方獲得信息反饋給我,我再盡快給他提供解決方案。”產品開發部負責人介紹,就這樣,2013年的春天,有8個小時時差的江南造船和Navigator公司人員,為初步方案的敲定頻繁進行著郵件溝通,有時一個晚上就是一二十封郵件。經過幾輪討論,2013年5月,租方對江南造船提供的船型方案基本認可,之后又經歷了近半年的等待,2013年12月,租方確定貨源后不久,江南造船正式與船東Navigator簽訂了4艘3.75萬立方米液化氣船的建造合同。
提前介入租家的需求是江南造船的研發思路。隨著美國頁巖氣產業的發展,乙烷作為伴生氣也有了不小的運輸需求。獲取了這樣重要的市場信息后,江南造船當即啟動了相關船型的研發工作。“不能等船東把什么都定下來了告訴你怎么做,再去研發。那時已經遲了,錯過了先機,船東可以選擇任何一家船廠建造。”研發人員表示,“在新的市場出現的時候,我們要做的就是根據市場需求、貨源需求、貨運需求,盡早介入船型研發,在船東尚不知道應該做什么船型的時候,我們給船東和租方提供解決方案。”
3挫折中破土成長
秉持著“用最小的船殼裝最大的罐”的設計理念,做好精度控制,將幾個“大塊頭”順利吊裝進艙,成為江南造船建造過程中的重點技術攻關項目。
液罐建造階段,制造方嚴控精度,對每個生產步驟作好精度記錄并建模,與船艙尺寸進行比對。2015年9月5~7日,江南造船對首制船的2號、3號液罐進行吊裝。當時氣溫在30攝氏度以上,用來固定液罐的環氧材料黏度明顯降低,流動性顯著提高,加上該船液罐較大,液罐鞍座線型很陡,導致鞍座內環氧在下落過程中發生流掛現象,為此,江南造船設計部同運行部、模塊部、品質保證部及液貨系統供應商TGE公司人員多次開會討論,制定了詳細的修補方案。
“我們從根本上尋找原因,通過1:1的模擬試驗來驗證方案的可行性,最終被妥善解決,也為后續姐妹船的建造提供了寶貴的經驗。”該船監造相關負責人說。
4成功的密性試驗
“Camel E”首制船,還是全球第二艘、國內首艘采用高壓主機系統和低壓燃氣系統的船舶,第一艘船由韓國現代重工承建,交付僅僅比該船早了幾個月。
據悉,該船配套了曼(Man)公司的高壓主機、瓦錫蘭的雙燃料發電機組、TGE公司的供氣系統。“在前期策劃階段,我們認為各系統之間的硬軟件、接口轉換會是一大風險點。”江南造船有關負責人介紹說,為此,江南造船召集曼公司、TGE、主機生產商現代重工等各方技術代表一起排查風險、梳理問題、提前策劃。“在各方的努力下,我們只用了3周的時間就完成了風險最大的主機燃氣調試,密性試驗一次完成,非常成功。”
相比之下,雙燃料發電機組的調試工作艱難得多,自系泊試驗開始至交船,發電機的問題貫穿始終。據了解,由于是新機型首次實船應用,發電機的特性試驗、負載試驗、燃氣調試試驗等都遇到了不小的技術難題。調試過程中,雙燃料發電機因控制系統問題導致點火油泵損壞,反復拆檢更換。同時,圍繞發電機的系統,低溫淡水、點火油管路、曲柄箱透氣、燃氣雙壁管、燃油循環泵管路都出現了更改,個別管路甚至更改了2次,現場施工難度大,且耽誤了調試周期。常規試航前后,船東自己聘請了專家對發電機的性能進行了測試,同時江南造船也相應添置了可以監測三相電壓和頻率的儀器,大大提高了效率。“為了保障工程進度,所有調試人員和管理人員24小時吃住在船上,不停工。”
5液氮冷罐 迅速又安全
今年7月,“Camel E”首制船開赴揚州進行LNG加注試驗。因該型船采用的是雙燃料的動力和電力系統,因此需要在甲板燃料罐內進行LNG加注,完成雙燃料主機和發電機燃氣試驗。江南造船此前成功完成了3萬立方米LNG船的LNG加注工作,但該型船的燃氣系統設計與之完全不同,經過充分的調研和討論,加注團隊決定選擇槽車-船的加注方式。
“看到我們對加液方案和應急預案進行了多次演練,供貨方對我們這個3萬立方米LNG船加注試驗的老班底豎起了大拇指。”江南造船有關負責人說。
7月4日,船舶按計劃靠泊加注碼頭,按照既定策劃方案有條不紊地進行著加注軟管吊裝、管路吹掃、密性試驗、氣體置換、燃氣罐預冷、燃氣加注、管路放殘、加注軟管拆除等作業流程。值得一提的是,加注團隊這一次開創性地采用了液氮來進行氣體置換和燃氣罐預冷,同之前普遍采用的LNG相比,液氮的冷罐效率更高,作為惰性氣體也更加安全。最終,原計劃需要5天的加注試驗僅耗時3天7小時就大功告成,為該船后續發電機和主機的燃氣試驗爭取了寶貴的時間。
首制船交付后,江南造船還有3艘“Camel E”半冷半壓式3.75萬立方米LEG運輸船在建。從最初的研發至今,已經歷了四輪冬夏,江南造船攻克了研發設計建造的重重困難,首制船鍛煉出了一支年輕給力的調試團隊,在30歲的調試班長的帶領下,2013年后進廠的小字輩挑起了整個燃氣系統調試的大梁。就像這支平均年齡不過27歲、由14人組成的核心調試團隊一樣,技術的不斷積累、傳承和超越,是江南造船全體員工最大的收獲。